HOW WE HELP
Issues & Tasks
Tag issues to equipment for visibility and analysis
- Assign issues and tasks to specific plant personnel creating accountability and visibility
- Capture photos and videos of the outage to speed issue resolution
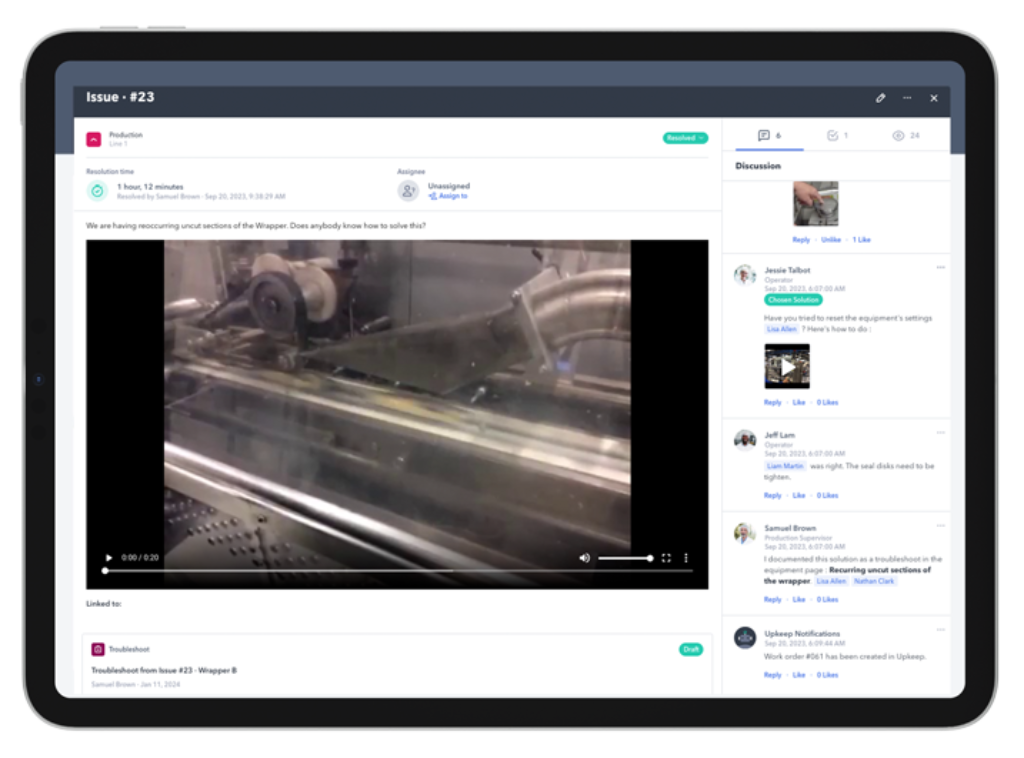