Your Guide to Manufacturing Training with a Connected Worker App
In this comprehensive resource, we explore the evolving landscape of manufacturing training and how modern solutions can enhance workforce development. You’ll gain valuable insights into the challenges and best practices for effective training, from overcoming skills gaps to creating an efficient learning environment. With actionable strategies and expert tips, this guide will help you understand how a connected worker solution can streamline training processes, improve on-the-job learning, and empower your workforce to meet the demands of today’s manufacturing environment.
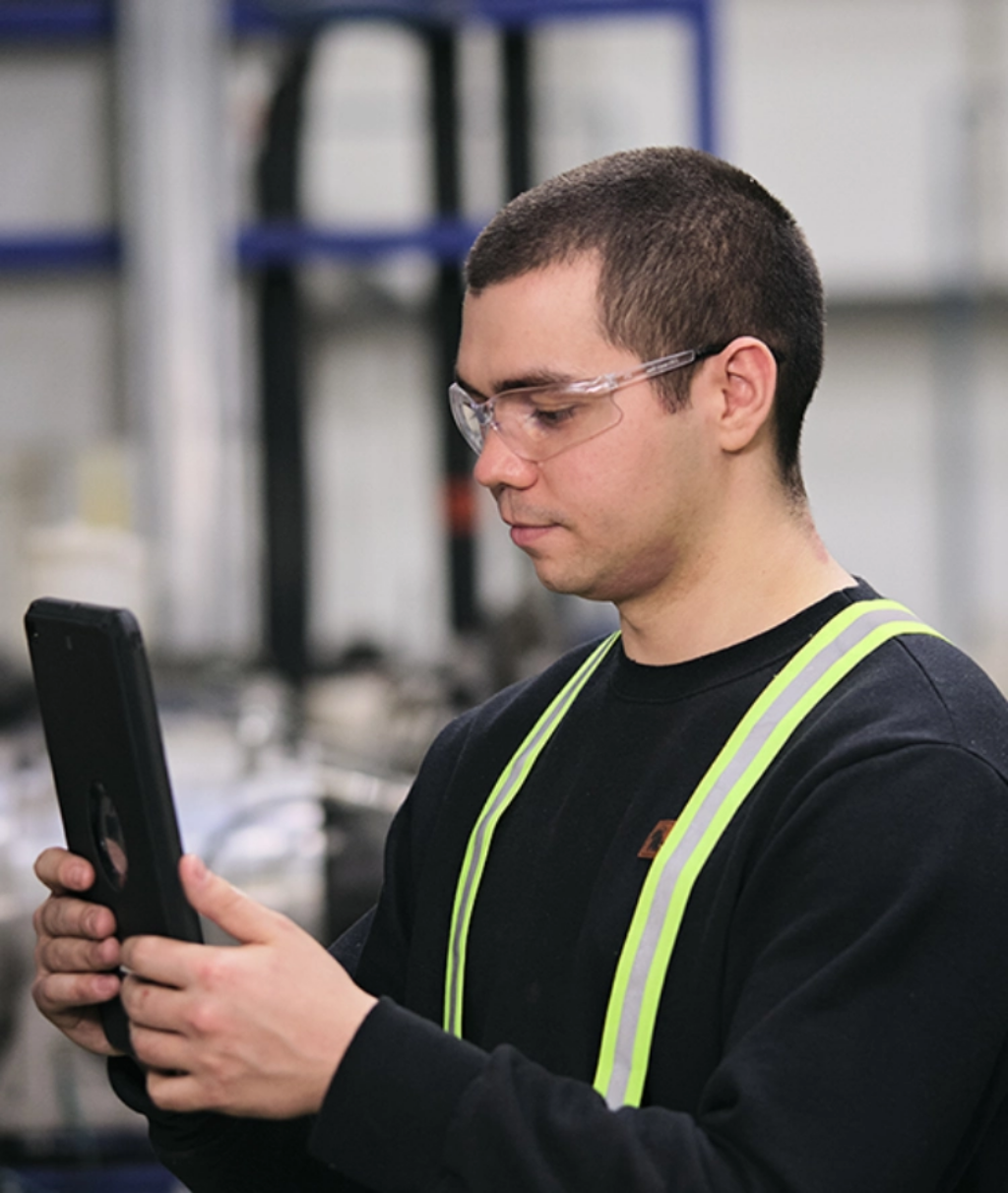